Warm Up Before You Run
Why conditioning your inlet parts after maintenance is good practice
- Eliminate background peaks and avoid costly reanalysis.
- Improve reproducibility and system performance.
- Document system cleanliness.
Introduction
Every good coach tells athletes to warm up before they run to make sure the body is primed for optimum performance. The same principle applies to maintaining your gas chromatograph—time spent warming up the analytical system after maintenance pays big dividends by improving accuracy and reducing the need for reanalysis. No matter whose products you purchase, inlet parts, just like columns, require a brief conditioning before they are ready for analytical work. Although it is tempting to save time by jumping directly into sample analysis after maintenance, warming up your system helps you get it right the first time. In this article, we will highlight inlet liners as a perfect example of the need to condition your inlet after maintenance to avoid costly coelutions, irreproducible results, and avoidable reanalyses.
Sources of Contamination
Most manufacturers of inlet liners take care to provide a clean product that will not exhibit chronic bleed or degrade your sample. However, even careful manufacturing, handling, and storage will result in a small degree of contamination on the liner or the wool packing inside the liner. Even the best liner can exhibit a small bleed pattern if it is used immediately after installation under typical chromatographic conditions.
Once the inlet liner is in a laboratory there are even more opportunities for it to become contaminated. Common sources of contaminants that can cause bleed include plastic packaging (e.g. phthalates used to make plastics more flexible) and oils from a person’s hands (e.g. fatty acids from finger oils). To evaluate bleed from contaminated liners, we first established a clean baseline with a control liner and then installed each test liner and ran the instrument without making an injection. Figure 1 illustrates the effect of handling an inlet liner with bare hands. Even some gloves will impart hydrocarbon contamination that can be very prominent and persistent (Figure 2). So, care needs to be taken when handling your new liners. Handling liners with clean forceps or with lint-free technical wipes is a good way to prevent liner contamination.
Figure 1: Eliminate contamination peaks from finger oils by warming up the system prior to sample analysis.

Column | Rxi-5ms, 30 m, 0.32 mm ID, 0.25 µm (cat.# 13424) |
---|---|
Standard/Sample | No sample injected; instrument ran the method conditions with no injection. |
Injection | splitless (hold 0.5 min) |
Liner: | 4 mm ID straight inlet liner w/wool, IP deactivated (cat.# 20782) |
Inj. Temp.: | 250 °C |
Purge Flow: | 40 mL/min |
Oven | |
Oven Temp.: | 50 °C (hold 5 min) to 320 °C at 30 °C/min (hold 10 min) |
Carrier Gas | He, constant flow |
Flow Rate: | 5.0 mL/min |
Detector | FID @ 330 °C |
---|
Figure 2: Hydrocarbon peaks from nitrile gloves are another example of contamination from maintenance activities that can be eliminated by warming up the system.
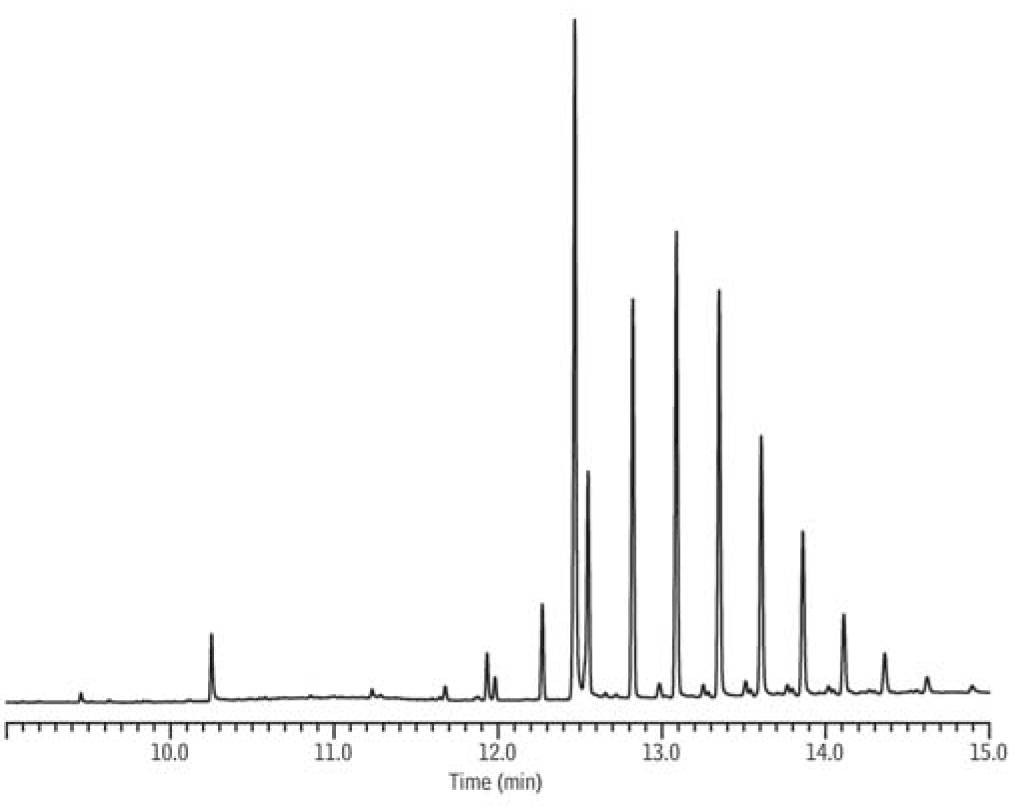
Column | Rxi-5ms, 30 m, 0.32 mm ID, 0.25 µm (cat.# 13424) |
---|---|
Standard/Sample | No sample injected; instrument ran the method conditions with no injection. |
Injection | splitless (hold 0.5 min) |
Liner: | 4.0 mm ID single taper inlet liner w/wool, IP deactivated (cat.# 22406) |
Inj. Temp.: | 250 °C |
Purge Flow: | 40 mL/min |
Oven | |
Oven Temp.: | 50 °C (hold 5 min) to 320 °C at 30 °C/min (hold 10 min) |
Carrier Gas | He, constant flow |
Flow Rate: | 5.0 mL/min |
Detector | FID @ 330 °C |
---|
Reduce Noise by Conditioning Your System
This contamination, also called background “noise” can be eliminated simply by conditioning the GC system prior to use. You can condition the entire inlet a variety of ways. One suggestion is to make a few preliminary runs using the analytical method parameters (inlet temperature, oven program, etc.) to be used in subsequent analyses. We evaluated several commercially available liners and determined that liner bleed generally will be gone by the second or third run (Figure 3). An advantage to this technique would be recorded data exhibiting the cleanliness of the liners and proof that the chromatographic system was clean prior to running actual samples. Another advantage for this technique is that it doesn’t exert any additional thermal stress on the system, which might mean longer lifetimes for parts such as inlet O-rings.
Figure 3: Warm up your system and invest in quality liners to reduce noise and improve accuracy.
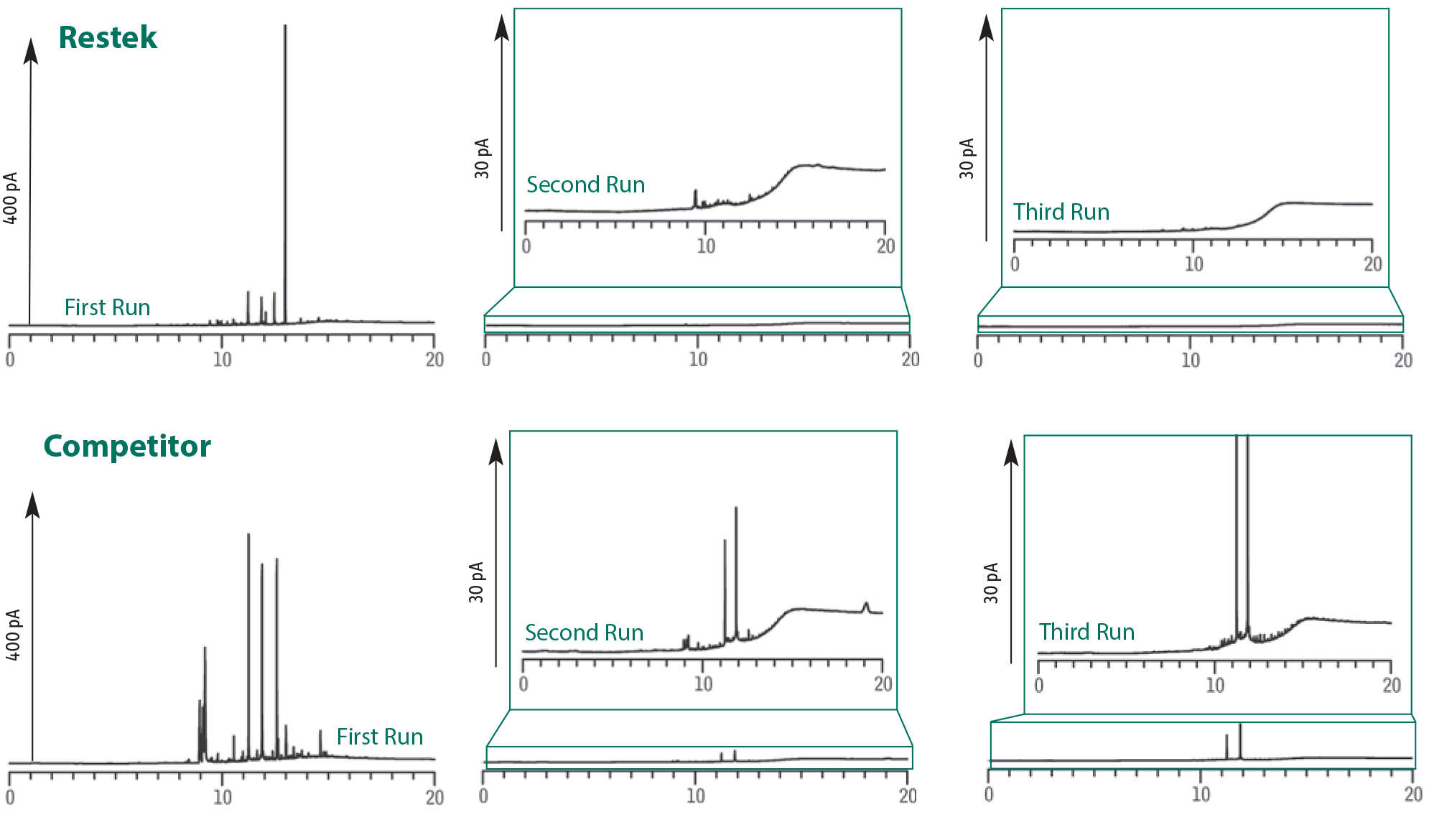
Column | Rxi-5ms, 30 m, 0.32 mm ID, 0.25 µm (cat.# 13424) |
---|---|
Standard/Sample | No sample injected; instrument ran the method conditions with no injection. |
Injection | splitless (hold 0.5 min) |
Liner: | 4 mm Split w/wool, IP deactivated (cat.# 20782) |
Inj. Temp.: | 250 °C |
Purge Flow: | 40 mL/min |
Oven | |
Oven Temp.: | 50 °C (hold 5 min) to 320 °C at 30 °C/min (hold 10 min) |
Carrier Gas | He, constant flow |
Flow Rate: | 5.0 mL/min |
Detector | FID @ 330 °C |
---|
Another method for conditioning your system prior to use is to elevate the thermal zones in your instrument for a set period of time. This “bake out” period will often get rid of any volatile or semivolatile contamination on new parts. The data in Figure 4 show that after just ten minutes of thermal conditioning a flat baseline is achieved and the system is ready for sample analysis. However, an important principle to remember with thermal conditioning is to use progressively hotter heated zones along the sample flow path. For example, your column should be hotter than your inlet, and your detector should be hotter than your column. This prevents condensation of any contamination, especially from the inlet onto the column. If condensation occurs, broad, poorly shaped peaks eluting at irreproducible retention times may be observed. These “ghost peaks” are semivolatile compounds that are gradually moving through the system with each analytical run.
Figure 4: Conditioning your system above method temperatures is an excellent way to remove contaminants.

Column | Rxi-5ms, 30 m, 0.32 mm ID, 0.25 µm (cat.# 13424) |
---|---|
Standard/Sample | No sample injected; instrument ran the method conditions with no injection. |
Injection | splitless (hold 0.5 min) |
Liner: | 4 mm ID straight inlet liner w/wool, IP deactivated (cat.# 20782) |
Inj. Temp.: | 250 °C |
Purge Flow: | 40 mL/min |
Oven | |
Oven Temp.: | 50 °C (hold 5 min) to 320 °C at 30 °C/min (hold 10 min) |
Carrier Gas | He, constant flow |
Flow Rate: | 5.0 mL/min |
Detector | FID @ 330 °C |
---|---|
Notes | System was conditioned for 10 min at the following temperatures: inlet 300 °C, oven 310 °C, detector 330 °C. |
Conclusion
We observed that no matter whose product you buy, you can expect some background noise if you install an inlet liner and immediately make a chromatographic run. However, with a little conditioning you will eliminate background peaks, document system cleanliness, and improve the performance of your system. Before analyzing valuable samples, take the time to warm up your system, ensuring that you are ready to run!